Establishing procedures and processes
Missed opportunities
In the past years, I have worked at several companies. And now as interim manager I work within even more companies. And I discovered that a lot of companies do not write down the processes, associated procedures or work instructions. Or they are outdated and/or not generally available.
What a waste! A missed opportunity. Because when your company / department has to deal with an increased workload and (temporary) new employees are deployed. There are no correct instructions on paper available. A lot of time needs to be spend on the explanation and guidance, while there is so much work already.
Where do you start
If you work with fixed steps, document it during your operations. Ask your colleagues take a critical look at it and store it digitally in a place that makes sense for all employees to find it. And check it on a regularly base, reflect and adjust if it is no longer applicable.
Small efforts, which can save a lot of time, for the moment a new colleague starts or someone must take over your work because you finally going on a deserved vacation.
Process management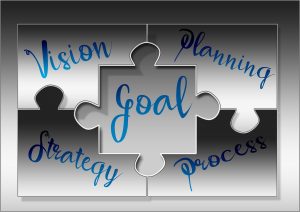
For senior management, the importance of process management is not always clear as well. If you want to know as a business owner what is happening within your organization and how efficient the process is. Or how a product or service is created and which people and equipment are needed in order to achieve this goal as effectively as possible. Documented procedures need to be available.
Documented procedures, work instructions and insight in the work & document flow is also required for ISO certification and maintaining ISO certification.
In my experience clearly visualized workflows and instructions can lead to more efficient processes. Therefore Process management and standardization will benefit the work output and quality.
So why not? Why not try to work more efficient, give better services to your employees and customers. And improve the quality of the input and output of your processes? When procedures are written down, it does not mean they should never change again and improvements are excluded. Whether it means additional work if things are documented, it is not I would say! It should save time.
Or maybe, if better quality is reflected in customer satisfaction and more orders are generated of course more work is generated…
Advice and supervision
As Quality & safety coordinator within a manufacturing company, I have gained much experience in analyzing and defining workflows, ISO procedures and certification. If you’re looking for supervision or in need of an adviser who looks objectively to your procedures. Please contact VAN EYCK ADVIES.